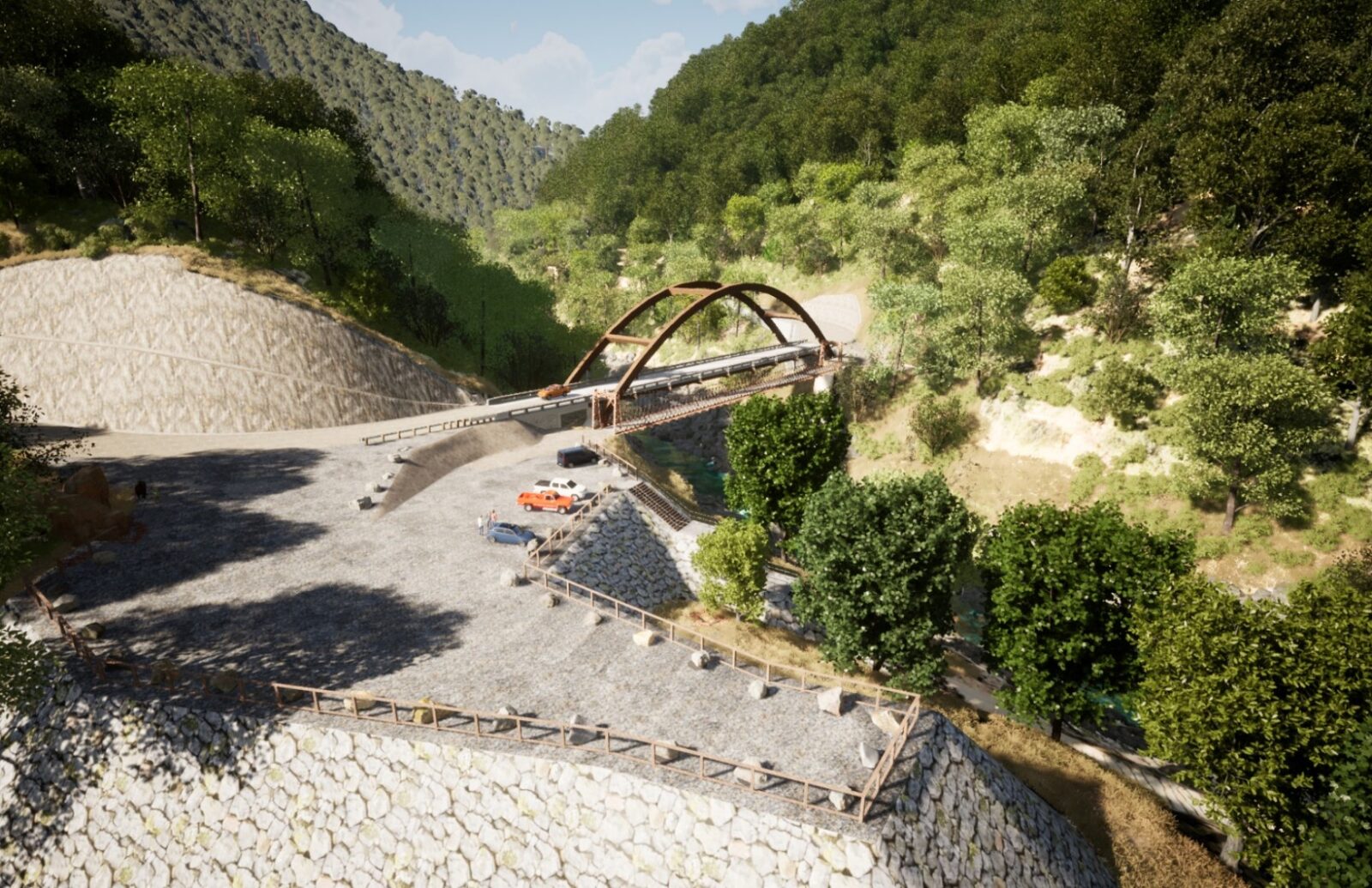
Four Benefits of CMGC Delivery: A Case Study on Historic Yankee Jims Bridge
Challenge: With a 3-ton load limit and limited emergency access across the North Fork of the American River canyon, the historic Yankee Jims Bridge could no longer meet the needs of Placer County’s residents and first responders. Replacing the bridge while preserving the historic structure—and minimizing environmental impacts in a rugged canyon setting—presented significant technical and logistical challenges.
Solution: Placer County selected the construction manager/general contractor (CMGC) delivery method to address the project’s complexity with greater flexibility and foresight. The collaboration between the County, Consor, and the contractor enabled the team to resolve key issues early in the design process. The project demonstrates how CMGC can:
- Reduce environmental footprint by identifying efficient construction access and minimizing disturbances.
- Leverage practical knowledge from contractor input to inform realistic, buildable design solutions.
- Implement innovative solutions in design and construction staging.
- Increase cost control and estimating accuracy by identifying risks and pricing them collaboratively.
Read the full white paper below. Director of Structures Mark Reno shares how early contractor involvement helped the team navigate steep terrain, protect sensitive resources, and preserve a piece of Gold Rush history—all while preparing for the needs of today’s communities.